NDTL Develops CO₂ Component Test Capability and Successfully Tests High Efficiency Transcritical CO₂ Compressor
NDTL Propulsion and Power (NDTL) has designed and built a closed test loop and a CO₂ storage and management system to support testing for supercritical and transcritical CO₂ power and thermal management components. The test loop can be installed in NDTL’s 10-megawatt, 5-megawatt, or 3-megawatt test cells to match the power, speed, and flow requirements of a particular test article. NDTL recently completed testing of the first stage of a high-efficiency multistage transcritical CO₂ compressor.
The development of high-efficiency compression systems is important for the design of CO₂-based power and heat pump cycles. Axial compressors inherently have higher efficiency compared to centrifugal and reciprocating machines, but they have not yet been tested or demonstrated using CO₂ as the working fluid. The high fluid density, high power density, and significant real gas effects present technical challenges in designing and testing an axial compressor.
With support from the U.S. Department of Energy (DOE), the team composed of NDTL, Echogen, and the University of Cincinnati is demonstrating the system efficiency advantages of utilizing axial compressors in renewable energy storage systems. This is being accomplished with the design and test of a 3-stage transcritical CO₂ axial compressor.
NDTL designed and fabricated the test loop, performed the mechanical design of the high-power density compressor, and is executing the test program. The University of Cincinnati, employing best practices from air-breathing compressors for aero-propulsion engines, performed the aerodynamic compressor design. Echogen leads the overall program and developed the transition path to a fielded system. Echogen has also provided its expertise in supercritical CO₂ systems.
The test loop consists of a variable speed drive motor, CO₂ inventory system, a heat exchanger between the CO₂ loop and the water/glycol loop, high accuracy Coriolis flowmeter, and cooling towers. The closed loop is installed in a test cell fully equipped with data acquisition and control systems.
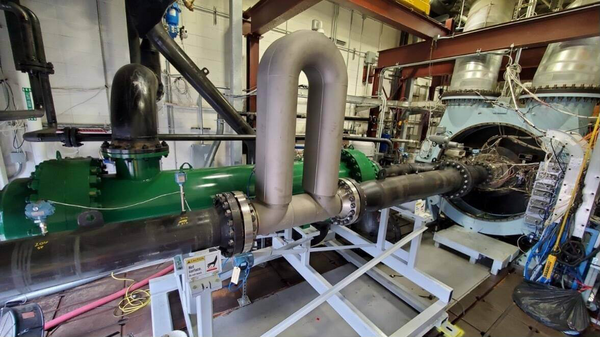
The initial testing of the first stage of the 3-stage axial compressor was completed at NDTL using the closed sCO₂ compressor test loop installed in the 10 MW cell. Steady-state conditions were obtained by removing enthalpy from the loop using a CO₂ – water/glycol heat exchanger. The nominal design speed, pressure ratio, and mass flow rate of the compressor are 19,800 rpm, 1.42, and 125 kg/s, respectively.
The compressor mapping test was performed from 60% to 100% corrected speed. The pressure ratio and the efficiency of the compressor were measured through the total pressure and total temperature rakes, which were installed at the inlet and the exit of the test compressor. All nine rakes were calibrated via an in-house flow calibration jet facility. The measured pressure ratio and the efficiency of the compressor aligned well with design predictions, and the measured isentropic efficiency of the compressor was above 90%.
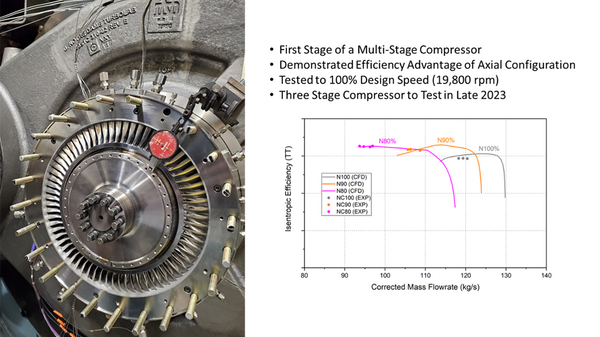
NDTL is preparing to begin testing of the 3-stage compressor. Updates are forthcoming.
Originally published by ndtl.nd.edu on November 27, 2023.
atLatest Research
- Brain tumor growth patterns may help inform patient care managementAssistant Professor Meenal Datta (University of Notre Dame/Wes Evard) A team of researchers from the University of Notre Dame, Harvard Medical School/Massachusetts General Hospital, and Boston University has developed a technique for measuring a brain tumor’s mechanical force and a new model to estimate how much brain tissue a patient has lost.
- Biseach Symposium Strengthens Cancer Research Partnership Between Notre Dame and University of Galway…
- Notre Dame announces new research collaborations with Ukrainian Catholic UniversitySeven faculty teams of collaborators from the University of Notre Dame (South Bend, Indiana, USA) and Ukrainian Catholic University (Lviv, Ukraine) have received grants from Notre Dame Global and Notre Dame Research to pursue…
- From reaction to resolution: The future of allergy treatmentTwelve-year-old Lauren Eglite was thrilled to attend a Notre Dame football game with her father, Erik, in 2017, even though her acute peanut allergy demands constant vigilance. She was even more excited when the stadium’s brand-new video board aired an NBC Fighting…
- New Study Highlights Mother-Child Link for Anemia in The GambiaAnemia is a "silent epidemic." It affects nearly 2 billion people globally, yet many people ignore its symptoms. Typically caused by the consumption of iron-deficient foods, anemia develops gradually. Its symptoms—such as fatigue, weakness, and shortness of breath—are frequently dismissed or misattributed.
- Megan McDermott joins ND–IBM Tech Ethics Lab as new Notre Dame directorThe Notre Dame–IBM Technology Ethics Lab, a critical component of the Institute for Ethics and the Common Good (ECG) and the Notre…